Right first time from 58% to 85% in two months.
A leading supplier of components to the international automotive industry approached us at a time when they were experiencing problems in quality and production efficiency. The automotive industry is unforgiving when it comes to quality and does not forgive mistakes, even in companies with an annual turnover of €500 million and almost 3.000 employees.
Achieved results
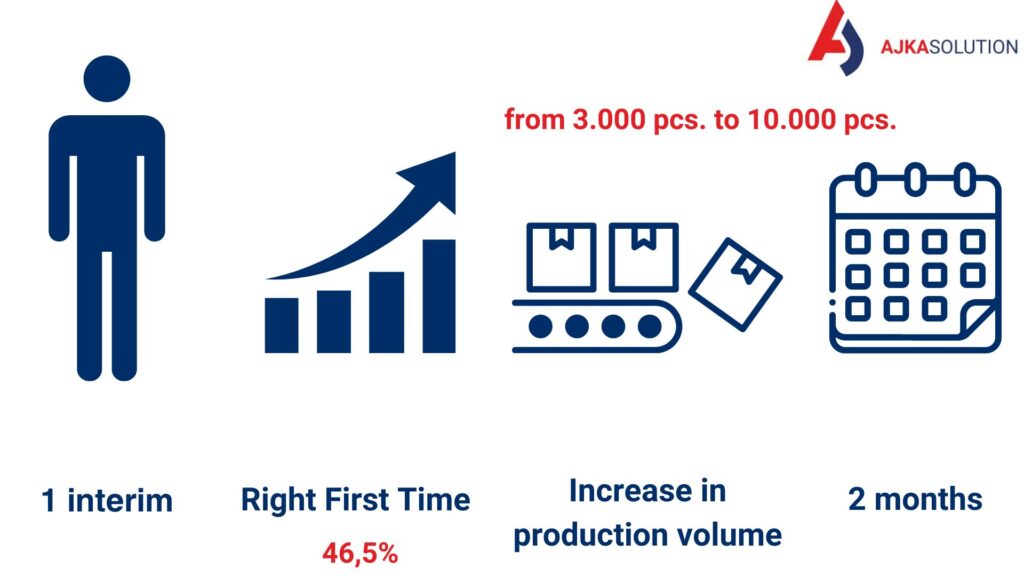
Our intervention increased the Right First Time indicator by 46.5%.
The customer was able to increase production volume to 10.000 units from the original 3.000 units per week.
The interim manager achieved all these results in just two months.
Project assignment from the customer
The client came to Ajka-Solution with a requirement to improve the required quality parameters and increase the efficiency of production processes. He needed to increase the volume of deliveries from the current 3000 to 10000 precisely defined car parts per week in six months.
Client default state
The company carries out series deliveries for a leading global automobile manufacturer. However, it does not meet the quality parameters of readiness for mass production. The low quality of the output causes:
- additional costs,
- the risk of delayed deliveries and
- the risk of not achieving the planned increase in delivery volumes.
The client is struggling with an overall low RFT (Right First Time) rate. The indicator for the percentage of products that are free of defects at first finalization is:
- 60 % for product A,
- 57,5 % for product B.
Our Plan
We employ an interim manager who has technical and organisational skills. The role of the interim manager is primarily project oriented with a focus on achieving change, problem solving and teamwork.
The first root cause analysis (5M: Man-Machine-Material-Method-Measurement) shows:
- lack of coordination, teamwork, problem prioritisation and inappropriate organisational structure,
- the problematic competence of the testing process,
- technical deficiencies in product design,
- unreleased purchased parts,
- overall lack of project readiness for mass production (APQP).
Key Factors
The project ran perfectly thanks to teamwork. The whole work was not just a one man show. A project team was formed on the customer’s side that was not afraid to step into the problems. From Ajka, the interim had the support of a wide team. To achieve success, we implemented a series of measures:
- We changed the organizational structure. We reorganised the management and prioritisation of tasks.
- We launched workshops focusing on the Root Cause Analysis (8D) problem-solving methodology. With these workshops, key issues affecting quality are surfacing faster.
We expanded quality control. We set up regular quality control and evaluation of purchased parts and daily monitoring of RFT trends. Identification of problems and non-conformities is thus accelerated and problems can be solved immediately.
- We spent time creating a comparative analysis of the testing process. With it, we identify weaknesses in the testing process and implement effective corrective measures.
What we have achieved
After the implementation of the measures, we are already achieving a significant improvement in quality parameters within 2 months. The RFT rate for product A has increased from the original 60% to 84% and for product B from 57.5% to 85%. With this success, the company is setting a new target to achieve in the next 2 months. RFT of 95% for product A and 98% for product B. In our view, the company is well on its way to achieving the new target.
What the customer says
The improvements have led to higher customer satisfaction for the company, but also to cost reductions and increased efficiency in production processes. According to management, this project showed the company how good planning can make the overall results better. The company’s management underlines the importance of coordination and its fluidity thanks to the new organisational structure.